Developing 3D printing technologies for manufacturing industry for more than 30 years, 3D Systems continues to offer its customers new products and business models in additive manufacturing with continuous innovation. The company recently announced its new plastics materials portfolio to the market. 3D Systems advertised its products designed for the company’s Figure 4 and Stereolithography (SLA) printing technologies in July 2020.
In the expanded product range; Figure 4 RUBBER-65A BLK, Accura Fidelity, Accura Bond, Accura Patch, and Figure 4 JEWEL MASTER GRY are included.
Menno Ellis, SVP and general manager, plastics, 3D Systems said that their team had continued developing new materials across their plastics portfolio to address a broader set of production applications. Ellis stated that they had maintained providing data sheets with key test results and performance specs to make it easy for their customers to make the optimal material choice for their needs. Ellis continued his words as follows; “Our material scientists and technical experts have leveraged decades of experience to engineer these high performing materials to deliver accurate, economical, and repeatable results to enable our customers to maintain competitive advantage.”
Each material offers a different solution
One of the new materials, Figure 4 RUBBER-65A BLK was specially formulated for additive manufacturing by addressing three key customer needs: Production Performance Properties, Production Mechanical Properties, and Production Testing Standards. This mid-tear strength elastomer was made as a material with high elongation at break for flexibility and durability. The material engineered for long-term environmental stability, is tested per UL94 standards. While these properties enable production of end-use elastomeric parts with a high degree of accuracy and minimal scarring from supports, at the same time this makes it ideal for applications such as air/dust gaskets, seals for electronics, vibration dampeners and pipe spacers.
Accura Fidelity, another material in the portfolio, has an ultra-low viscosity. Accura Fidelity is an antimony-free stereolithography (SLA) resin with clean burnout. This product was designed to create patterns for a variety of castable metals. Accura Fidelity, also including titanium and aluminium alloys; when used as part of 3D Systems’ QuickCast process, enables rapid creation of medium to large, lightweight, and easy-to-handle casting patterns – leading to increased casting yields. 3D Systems has also introduced Accura Patch and Accura Bond, a new UV curable class of post-processing materials. Accura Patch, a high viscosity material, was designed to fill QuickCast pattern drain holes during post-processing. Accura Bond, also a high viscosity material, was created to join various printed patterns together into one large pattern.
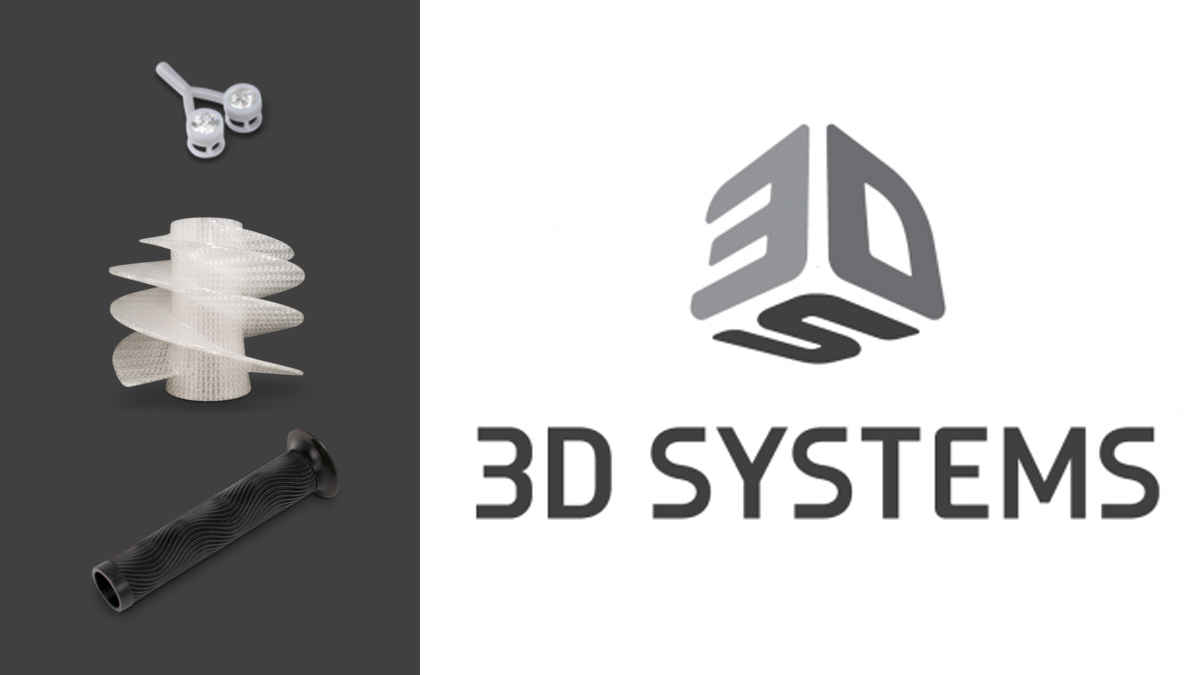
Figure 4 JEWEL MASTER GRY was specially designed and optimized as a solution for the burgeoning 3D printed jewellery market. The product is created to address three application-specific workflows: jewellery casting patterns, master patterns for molds, and prototype/fit check models. The product was well suited for producing high definition master patterns for making silicone or RTV molds; especially for high volume, mass production of designs. It is stated that this material also delivered exceptional precise surface quality for design and functional prototyping; as well as snap-fit and stone-in-place testing. In addition, Figure 4 JEWEL MASTER GRY meeting biocompatibility standard ISO 10933-5 for cytotoxicity; made it safe for try-ons and fittings.