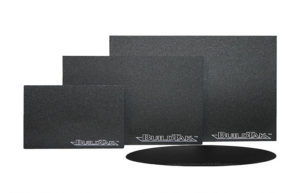
Signing a great print goes through some conditions. Setting the print calibrator correctly, selecting the appropriate filament, an effective software … The list can be extended. The product removal process, which is the last step in these conditions, is also very important. FlexPlate, which is the latest generation of production, is a very practical and very effective solution.
You’ve done your design, print adjustments, filament selection, X-Y-Z axis measurements. The result looks good, but there is a tiny problem; your print sticks to the platform and you can not get it out. This problem, which happens to many printer owners with FDM technology, usually ends with the damage of the bottom surface of the product. But not anymore! How? Let’s ask BuildTak.
BuildTak is a team that comes together to solve the problems that arise during and after printing in 3D production. Prior to that, the team that provided adhesive surfaces to adhere to the printing platform of the first layer from the nozzle, which was a further printing problem, favored many FDM users with this latest innovation. As a result of the heat on the print platform, the team developed the FlexPlate system to ensure that the printed product easily comes off. This three-part system is simple to install and use.
Easy with FlexPlate
This system, which consists of a magnetic base with a magnetic property, a resilient red printing plate and a sticky surface, needs to be assembled first. First of all, you spend the magnetic field on the printing platform of your printer. Then you stick a flexible red mold on the adhesive surface. The already tacky surface coating will immediately sit on the flexible printing plate. You put this layer on top of the magnetic base with the black coating facing up. Remember that the black part must be the part that the nozzle touches. There is no slipping or swaying during printing due to the red printing pattern sticking to the base due to magnetic.
After installing your FlexPlate system, there is one more important thing you need to do. It also changes the setting of your Z axis. These layers that you place on the press platform are about 3mm. If you reset the Z axis in this direction, you will not experience problems such as striking the nozzle during printing. Your printer is ready for printing after these steps!
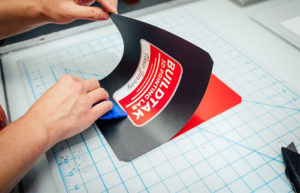
With a few bending movements
This product can be easily removed from the printer after production is finished and can be easily removed by applying bending movements to the left and right, back and forth. Thanks to its flexible structure, the red layer is repeatedly bent, but it is left unabated again. The flexible and magnetic layer is used more than once, but another buildTak product, the surface coating, needs to be changed for each print.
This innovation, which solves the problem of surface irritation seriously while removing the print; provides convenience to the user while reducing the risk of product failure and saving. Only the magnetic base of the FlexPlate system, which is described as compatible with all FDM printers; is manufactured specifically for each printer. With dimensions ranging from 139 x 139mm to 304 x 304mm, addition to this package the BuildTak team also developed a spatula that would make it easier to remove the product. The new FlexPlate and additional materials seem to be indispensable for makers who are perfectionists in print and who use the raw materials wisely.
You can order this package from BuildTak web address. The price of the product differs according to its size.