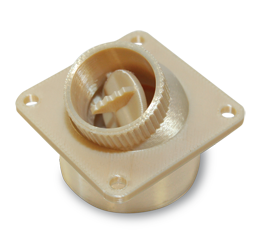
Adopted as a global leader in aircraft production, Airbus has produced some parts of its new A350 XWB aircraft with FDM technology. The company relied on Stratasys service in printing, and also used ULTEM ™ 9085 as for their raw material selection.
The prominence of 3D printing in the aviation industry is increasing. From the beginning, aircraft manufacturers interested in this technology are working to minimize material, cost and time. One of these manufacturers has benefited from Stratasys ULTEM ™ 9085 resin for the new model A350 XWB.
The French-based company is known for its pioneering innovations in the aviation world. Starting their additive manufacturing journey with Stratasys in 2014, a significant portion of the A350 XWB model was produced by Stratasys’ FDM solutions. Having a significant advantage in this regard, the aviation leader also received service from Stratasys in the post-production period.
After this cooperation, company material experts started to examine the additive manufacturing solutions in more detail and started to try different raw materials for this model. In this context, the company’s engineers approved Stratasys’ ULTEM ™ 9085 resin for FDM technology, and the A350 used this resin for XWB parts.
Airbus obtained flexibility
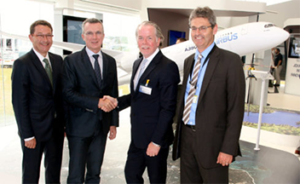
The A350 XWB is highly anticipated by the aviation industry to perform its first trial flight in China; between October 29 and November 8. Thanks to FDM technology and ULTEM ™ 9085; the company has achieved a new level of flexibility in the production and wasted materials.
Stating that a leader like Airbus is pleased to add Stratasys solutions to the industry network; Stratasys President of EMEA (Europe-Middle East-Africa) region Andy Middleton said; 3D benefits are increasingly becoming one of the parts of production chain. Midlleton added; “We see a significant increase in demand for additive manufacturing solutions. Many industry giants who are sensitive about time; and want to present the best to their customers are now heading to 3D.”