ABS and PLA… If you ever make a research on 3D printing you definitely heard these plastics. These materials which are highly demanded in 3D world, have fundamental differences even though they seem similar. Accordingly, ABS comes to the forefront in one applications when PLA provides advantages.
Being the most accessible and most used print technique FDM(Fused Deposition Method) meets different demands with different material options. ABS(Acrylonitrile Butadiene Styrene) and PLA(Polylactic acid) are the most popular materials of this printing technique. Even though they are similar in general, these materials show differences in various conditions.
Moisture laden ABS will tend to bubble and spurt from the tip of the nozzle when printing; reducing the visual quality of the part, part accuracy, strength and introducing the risk of a stripping or clogging in the nozzle. ABS can be easily dried using a source of hot (preferably dry) air such as a food dehydrator. PLA responds somewhat differently to moisture, in addition to bubbles or spurting at the nozzle, you may see discoloration and a reduction in 3D printed part properties as PLA can react with water at high temperatures and undergo de-polymerization. While PLA can also be dried using something as simple as a food dehydrator, it is important to note that this can alter the crystallinity ratio in the PLA and will possibly lead to changes in extrusion temperature and other extrusion characteristics. For many 3D Printers, this need not be of much concern.
Both ABS and PLA also smell while printing, as heating the thermoplastic gives off fumes. That said, it’s the print temperature that primarily affects intensity of said fumes — not so much the material itself. Yes, ABS will smell like hot plastic and require ventilation while PLA will smell mildly sweet, but the strength of these smells is going to be dependent on your printer.
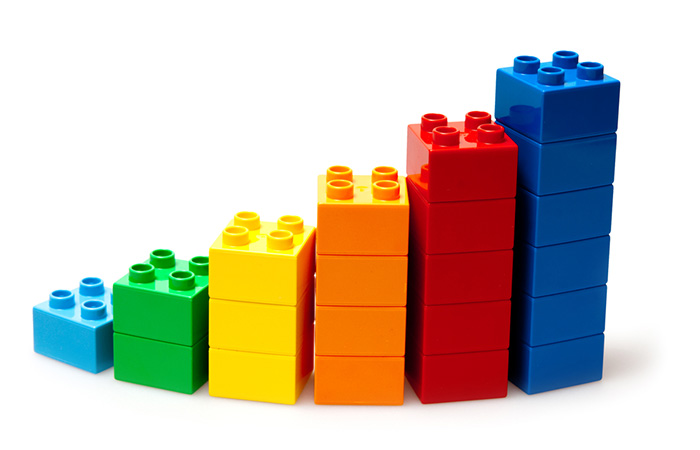
For fine features on parts involving sharp corners, such as gears, there will often be a slight rounding of the corner. A fan to provide a small amount of active cooling around the nozzle can improve corners but one does also run the risk of introducing too much cooling and reducing adhesion between layers, eventually leading to cracks in the finished part.
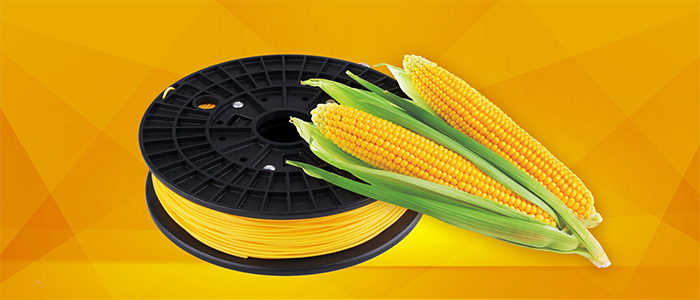
PLA undergoes more of a phase-change when heated and becomes much more liquid. If actively cooled, much sharper details can be seen on printed corners without the risk of cracking or warp. The increased flow can also lead to stronger binding between layers, improving the strength of the printed part.