3D manufacturing shows its superior quality in nuclear power plants where durability and safety is crucial.
Being very active in 3D sector with digital solutions as well as manufacturing projects, Siemens made a first in Krško nuclear power plant. 3D printing an impeller for fire protection pump, the firm proved its pioneer in innovation once again.
The replacement part produced for the Krško nuclear power plant in Slovenia is a metallic, 108mm diameter impellerfire protection pump for a fire protection pump that is in constant rotating operation. The water pump provides pressure for the fire protection system at the plant. The original impeller was in operation since the plant was commissioned in 1981; its original manufacturer is no longer in business. Obsolete, non-OEM parts are particularly well-suited for this new technology as they and their designs are virtually impossible to obtain. This technology thus allows mature operating plants to continue operating and achieving or, as in the Krško case, even extending, their full life expectancy.
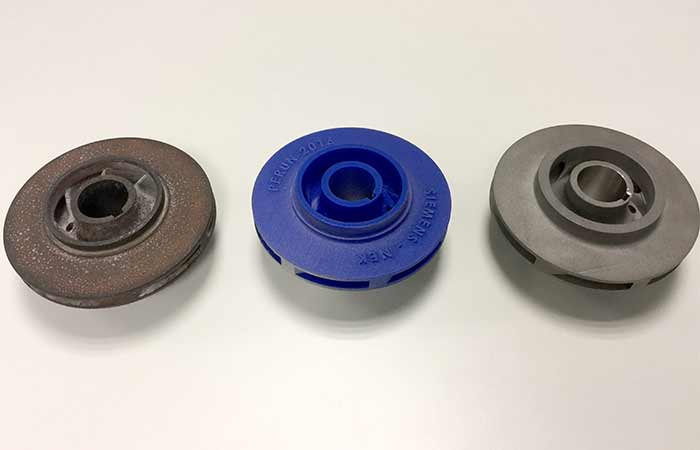
Siemens’ team of experts in Slovenia reverse-engineered and created a “digital twin” of the part. The company’s additive manufacturing (AM) facility in FinspÃ¥ng, Sweden, then applied its advanced AM process using a 3D printer to produce the part.
“We continue to push forward our investments and cutting-edge advancements in additive manufacturing and 3D printing,” said Tim Holt, CEO of Siemens Power Generation Services division. “The better than expected performance of this 3D-printed part gave us confidence that we can reach the full life expectancy from our asset,” said Vinko Planinc, Head of Maintenance at the KrÅ¡ko plant. “Siemens has a long history of innovation in this area and their dedication to providing their customers with the latest, proven innovations made them an excellent partner for this project.”