The artificial intelligence (AI) software Peregrine was developed by ORNL (Oak Ridge National Laboratory) researchers, the largest science and energy laboratory of the US Department of Energy. Peregrine collects and analyses data through every step of the 3D printing manufacturing process using a custom algorithm. Designed for powder bed 3D printing machines, Peregrine offers solutions to problems that cause defects in the layer surface during the printing process. This allows Peregrine to achieve new levels of automation and manufacturing quality assurance; while eliminating the need for expensive characterisation equipment.
The Peregrine software uses a custom algorithm that processes pixel values of images; taking into account the composition of edges, lines, corners and textures. Providing detailed data during the printing process; Peregrine automatically alerts operators to make adjustments when it detects an anomaly that may affect the quality of the part. Vincent Paquit, who leads advanced manufacturing data analytics research as part of ORNL’s Imaging, Signals and Machine Learning group, explained the process as follows; “Capturing that information creates a digital “clone” for each part, providing a trove of data from the raw material to the operational component. Then we use that data to qualify the part and to inform future builds across multiple part geometries and with multiple materials; achieving new levels of automation and manufacturing quality assurance”.
AI software Peregrine offers solutions to the inabilities of conventional manufacturing
During the printing process, problems such as uneven distribution of the powder or binding agent, spatters, insufficient heat, and some porosities; can result in defects at the surface of each layer. Some of those issues may happen in such a very short timeframe that they may go undetected by conventional techniques. ORNL, Principal Investigator for Peregrine, Luke Scime, told that one of the fundamental challenges for additive manufacturing is that you’re caring about things; that occur on length-scales of tens of microns and happening in microseconds. Scime noted that because a flaw can form at any one of those points at any one of those times; it becomes a challenge to understand the process and to qualify a part.
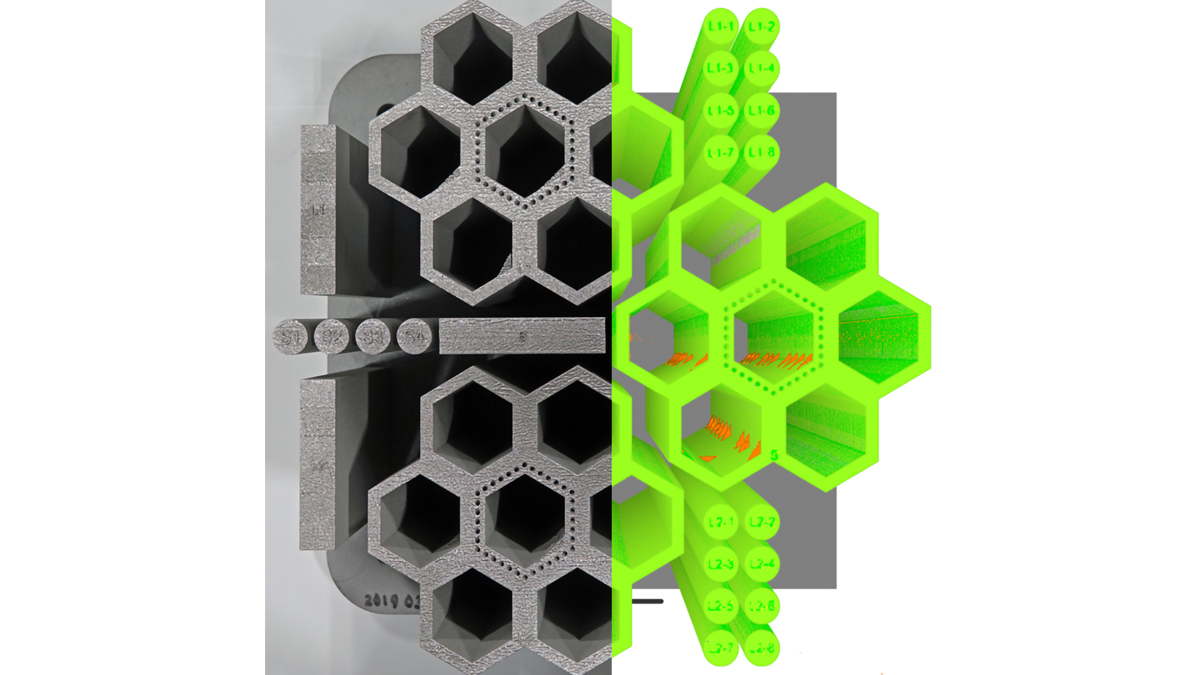
However, ORNL researchers created a novel convolutional neural network; a computer vision technique that mimics the human brain in quickly analysing images captured from cameras installed on the printers. While it enables to have a 3D map of each pixel; it offers an important opportunity to understand the build process. The AI software has been tested successfully on seven powder bed printers at ORNL so far. Peregrine produces a common image database that can be transferred to each new machine; to train new neural networks quickly, and it runs on a single high-powered laptop or desktop.
Peregrine allows parts to be uniquely identified
Scime stated that as the monitoring system has evolved, researchers are able to combine the image data; with data from other sources such as the printer’s log files, the laser systems and operator notes. Scime said that this allows parts to be uniquely identified and statistics from all parts tracked and evaluated. ORNL researchers also emphasised that by making Peregrine software independent of machines; printing manufacturers can save development time while offering an improved product to the industry.
It contributes to “digital thread” that supports the factory of the future
The software, named Peregrine, supports the advanced manufacturing “digital thread” being developed at ORNL that collects and analyses data through every step of the manufacturing process; from design to feedstock selection to the print build to material testing. The digital thread supports the factory of the future in which custom parts are conceived using computer-aided design, or CAD, and then produced by self-correcting 3D printers via an advanced communications network; with less cost, time, energy and materials compared with conventional production.