Industrial manufacturing company, Sodick offers one solution for various applications by combining milling and 3D printing.
Performing many applications from milling to metal 3D printing; electrode machining and EBM polishing, Sodick continues to expand its solution range with many innovative technologies. Bringing milling and 3D printing together, the company produced and hybrid machine to offer both technique’s advantages.
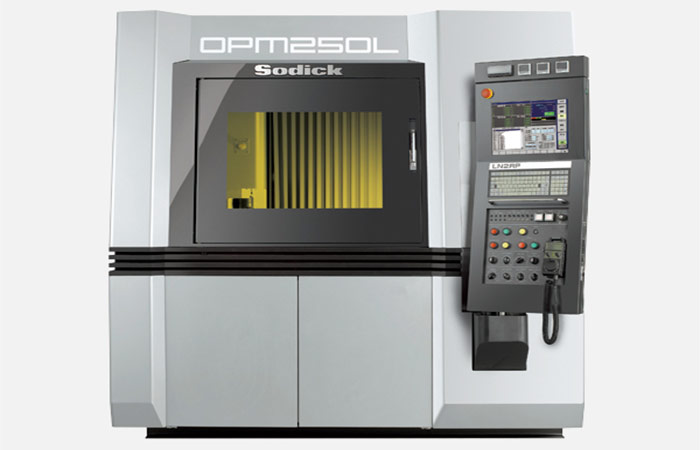
The machining enables the continuous process of melting by the irradiation of metallic powder with laser light followed by finish machining by milling with rotating tools.
In particular, for die manufacturing for plastic molded products, complex shapes such as three dimensional cooling channels and deep ribs can be manufactured with this single printer.
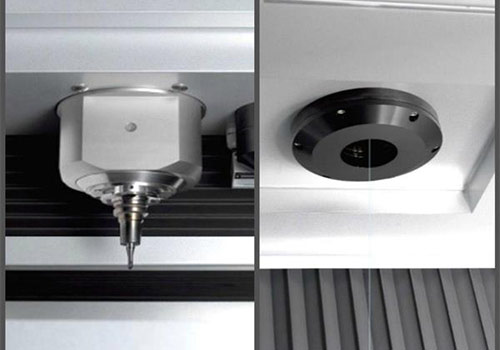
With a build volume of 250 x 250 x 250 mm, Sodick’s machine is ideal for manufacturing relatively small but highly complex metal parts. By combining 3D printing with milling technologies, the company explains it can offer parts with higher precision. Moreover, the DMLS process can create parts with up to 99.99% density, and the subsequent milling process allows for standard cutting to a 2-micron Ra surface finish, as well as a shift cut that offers 0.47-micron.
The OPM250L also enables machining workpieces before printing is complete, making it possible to alternate laser sintering and milling passes. In addition to its usefulness in producing conformal cooling channels, this capability also helps reduce the number of parts necessary to produce a mold. Also significant is the machine’s ability to manufacture in a single print what would normally take multiple individual parts to make up. So OPM250L can make a complex mold, usually made from 21 individual pieces, in a single print. “Saving a significant amount of time and providing advantage, OPM250L will offer solutions for manufacturers” as the company stated.