Honeywell, a Fortune 100 company (a list of the top 100 companies in the United States), announced that the flight-critical engine part manufactured using additive manufacturing technology has received approval from the FAA (Federal Aviation Administration). The part is very costly and difficult to make with conventional manufacturing methods, but it is produced in a shorter time and easier way thanks to 3D printing technology, while at the same time providing cost saving. In addition, Honeywell also offers solutions to the sourcing and supply chain problems of the 3D printed parts.
Honeywell started metal additive manufacturing operations in its laboratories at Phoenix in 2007. Finally, the critical flight-engine part manufactured with 3D printing was approved by the FAA, with which it was in close contact during the working process. The part, known as the #4/5 bearing housing, is currently in production and was installed on an in-service engine. It is a major structural component in the ATF3-6 turbofan engine used on the Dassault Falcon 20G maritime patrol aircraft using by the French Navy for patrol and search-and-rescue missions. Designed by Garrett in the 1960s and certified in 1967, there are only about a dozen ATF3-6 engines still in use. This leads sourcing and supply chain challenges for operators of Dassault Falcon 20G aircraft.
The part is very difficult to make with conventional methods. In this way, the molten metal is poured into a mold and allowed to harden, and goes through a complex production process. For this reason, the tools used in this process increase the cost significantly. However, thanks to additive manufacturing, these parts can be printed much faster and in smaller quantities without the need for expensive tools. During this process, components are built from the bottom up; with layers of powdered metal fused on top of one another using a laser.
Manufacturing time is reduced from 2 years to 2 weeks with 3D printing
Honeywell Aerospace Vice President of Manufacturing Engineering, Jon Hobgood stated that though there aren’t many in service; Honeywell is responsible for supporting and maintaining these engines, and he added; “We had to find a way to address these supply chain issues and keep these aircraft flying”. Hobgood noted that they had been able to use their expertise in additive manufacturing; to produce the qualified part much faster, reducing their lead time from approximately two years to two weeks.
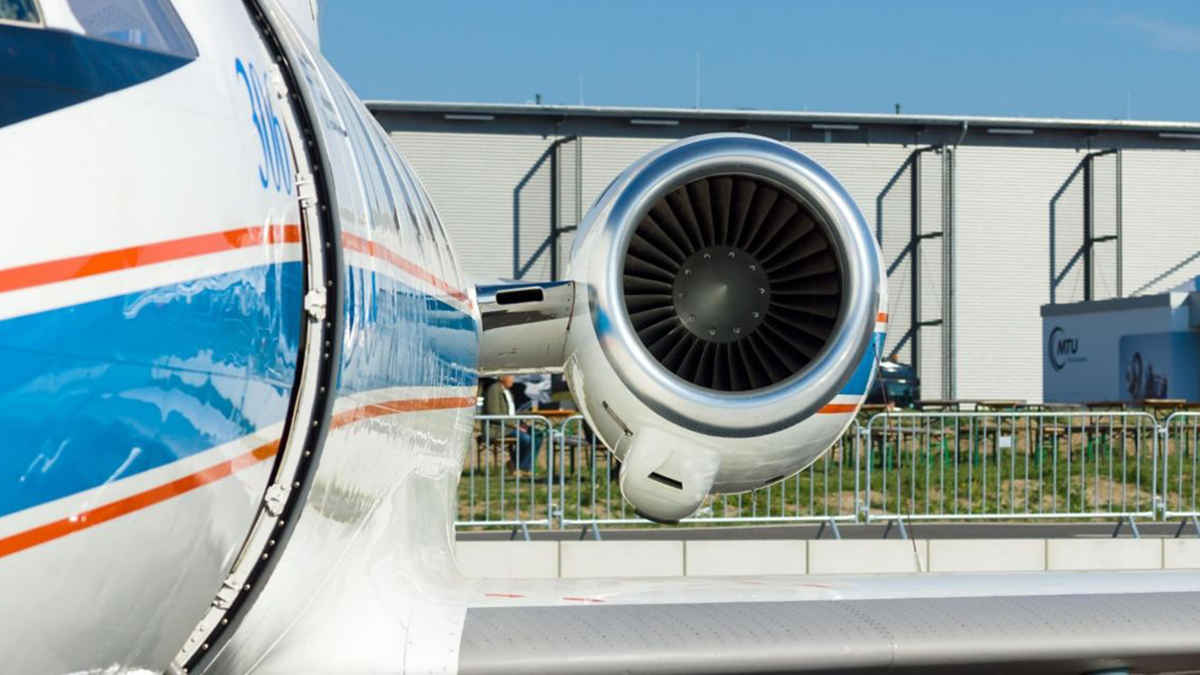
It also is a major win for the additive industry
Telling that this is a major milestone for Honeywell, Jon Hobgood said; “Because it demonstrates the maturity of our additive manufacturing operations; and paves the way for us to print more certified, flight-critical parts in the future”. Stating that it also is a major win for the additive industry; Hobgood said that as flight-critical parts face heavy scrutiny and high standards for qualification and installation on aircraft; but this shows it can be done.