While celebrating its 25th anniversary, JPB Système announced that it has sold the 250,000th borescope plug along with the 500,000th LULYLOK self-locking device anticipated at the end of the year. The leading manufacturer of efficiency-enhancing technology solutions for aerospace, aeronautic and other industries, the company serves some of the industry’s largest manufacturers with Industry 4.0 based processes, including Safran, Pratt & Whitney, GE, Rolls-Royce, and ITP Aero. Focusing on self-locking solutions, the company also recently announced that it has developed a middleware solution to empower companies that want to adopt intelligent manufacturing and the Industry 4.0 revolution.
JPB Système have recently surpassed the sale of its quarter-of-a millionth borescope self-locking plug, and is well on track to hit another landmark with production of its half-a-millionth LULYLOK B-nut self-locking device. JPB Système first designed the product to solve a specific problem that aerospace giant Safran had passed on to the company in the 1990s. Borescope self locking plug eliminates the need for lockwires when securing an engine’s connections prior to visual inspection. The product that the company has been developing since then, is still widely used today by Safran as well as other aircraft engine manufacturers such as Rolls Royce and Pratt & Whitney. JPB’s borescope self-locking plugs provide a safe and secure seal for the various borescope inspection ports situated around the turbine engine case.
JPB Système offers customers a system that reduces maintenance time from 1 hour to 10 seconds
JPB Système now holds a large part of the market, with the product certified on a range of aircraft engines; including the GE90-115 engine for the Boeing 777 and the G7200 engine for Airbus’ A380. The company’s customers also have access to a significantly more efficient system that reduces maintenance time from one hour to just 10 seconds. JPB Système CEO, Damien Marc said that the world’s foremost aircraft engine manufacturers quickly and wholeheartedly had embraced these products. Marc stated that the way of this embracement is testament to their ability to improve safety; and remove labour intensive processes in support of more efficient MRO processes, and added; “We are extremely proud to achieve such an impressive double milestone; especially as we celebrate a quarter of a century serving the world’s foremost aircraft engine manufacturers”.
Another popular solution of JBP Système is LULYLOK. As an advanced B-nut for fittings, it features a unique self-locking device that ensures sealing of pipes; thereby preventing loosening and leakage caused by severe vibration and extreme thermal conditions. Like the borescope plug; LULYLOK addresses safety concerns by eradicating the need for a lockwire or safety cable; to secure the threaded parts within the engine. In this way, foreign object damage is eliminated while maintenance costs and installation time are reduced. Thanks to these unique attributes and benefits; JPB continues to expand the use of LULYLOK beyond aerospace and into the automotive, railway and nautical industries.
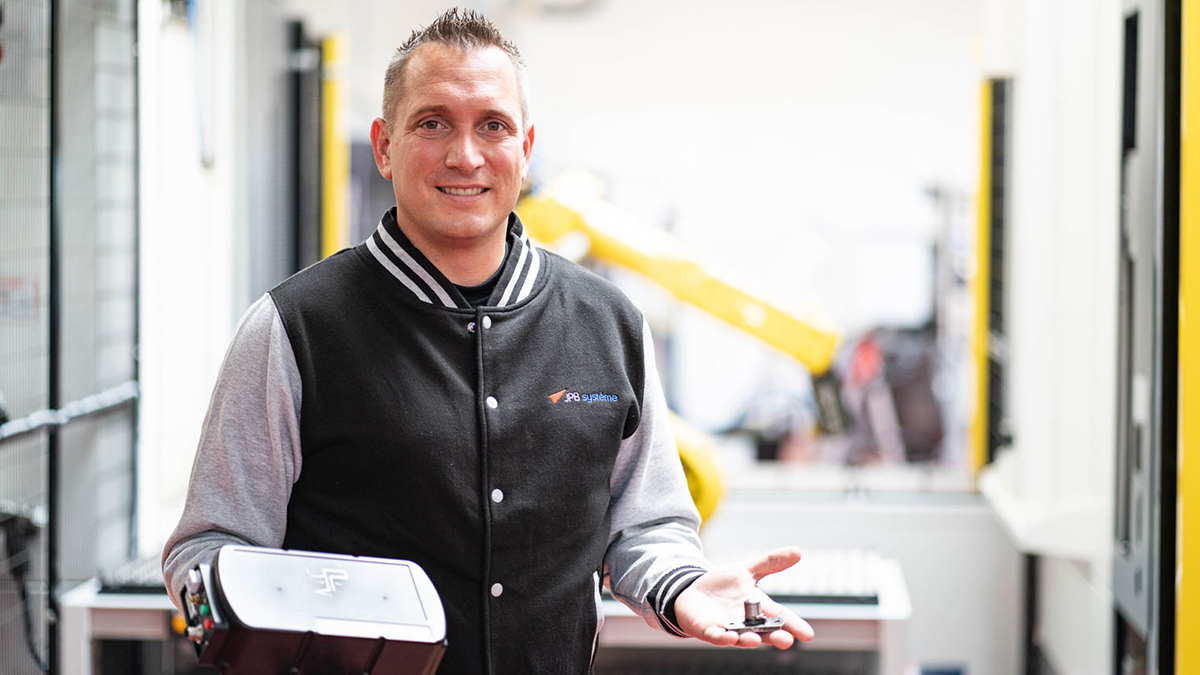
New solution to companies being on course for Industry 4.0: KEYPROD
Despite a heritage in the creation and delivery of self-locking solutions for aircraft engines; JPB Système recently developed a pioneering middleware solution designed to empower those companies; seeking to embrace intelligent manufacturing and the Industry 4.0 revolution. The innovative manufacturing execution system, known as KEYPROD, enables manufacturers to; connect, track and measure the effectiveness of all elements of the production process, including machinery and associated applications. Early adopter trials of KEYPROD are currently underway with several companies, with commercial availability of the solution expected in 2021.