Supporting 3D technology with material production, TreeD presented P-LENE filament to the market stated to be advantageous in molding and functional production.
Italian based TreeD continues to its journey with new materials offering durability and quality. The company aims to increase its market influence with P-PLENE polypropylene filament emphasizing functionality.
There are a number of advantages that accompany the use of 3D printing technology, from cost effectiveness to faster production times. But one area that the technology slightly lacks is in material functionality, which oftentimes fails to meet the strength and resilience of the injection molding process.
TreeDโs new polypropylene-based filament offers 95% of the material characteristics of an injection molded object, including high mechanical strength, toughness, wear proof, and chemical resistance. P-LENE was specifically formulated for 3D printing purposes, and is both easy to use and odorless. The TreeD team, which was born out of the plastic extrusion company SA2P Xtrusionplastics, spent over a year studying and developing the filament.
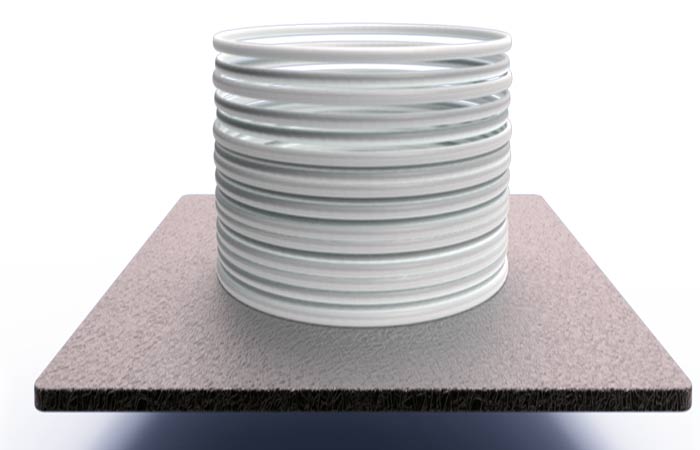
Although the P-LENE filament is mechanically superior to many other standard materials, theprint settings are quite normal. TreeD recommends a plate temperature of around 100ยฐC, a nozzle temperature of 245ยฐC, and a print speed of 60-70 mm/s. There are a number of great features that TreeD boasts about their latest material. Not only does it provide high impact and chemical resistance, it also prevents water absorption and doesnโt break under stress. The P-LENE is also recyclable, and can safely come in contact with food, skin, and pharmaceuticals.
By reformatting the widely used polypropylene polymer for 3D printing, TreeD is helping to push 3D printing technology to greater heights. By offering a filament that provides nearly the same strength as injection molding, more designers and manufacturers will be able to utilize 3D printing technology and expect superior material properties.