NeuBeam technology developed by the UK based Wayland Additive offers a solution to the limitations of the current laser and eBeam (electron beam) PBF (Powder Bed Fusion) metal additive technology. Designed with NeuBeam technology, Calibur 3 provides monitoring and intervention during printing thanks to its monitoring feature. In additive manufacturing, it eliminates the residual stress problem leading to fracture, especially in the production of large parts.
The company continues to develop NeuBeam technologies to overcome the problems manufacturers face in current metal additive manufacturing processes. As a result of these works, Wayland Additive has finally announced that it will launch Calibur 3 on January 27, 2021. CEO of Wayland Additive Will Richardson said; “Save the date in your diary now. We are in the process of curating an impressive in-person and on-line event which will be of huge interest to industrial sectors that use or are planning to use metal AM for production applications,” and he noted that January 27 would be a pivotal day for Wayland. In addition to this, Richardson told that this would be also a pivotal day for the industry as they got a first clear view of the opportunities that exist through the use of their NeuBeam technology.
The advantages of NeuBeam technology
One of the most important advantages of NeuBeam is that; it eliminates the residual stress problem in conventional electron beam PBF processes. Calibur 3 is defined as a hot part machine, not a hot bed machine; as high temperatures are applied only to the part, not the bed. In this way, the machine offers a solution to the residual stress problem experienced during the traditional electron beam PBF process, resulting in deformation and sometimes even fracture.
With the elimination of these problems that are mostly seen in large-scale printings; it seems possible to large-scale manufacture without residual stress, that cannot be realized now. This feature of the machine also saves energy and costs, enabling the reuse of unused materials after printing. In addition, it makes the post-printing process easier.
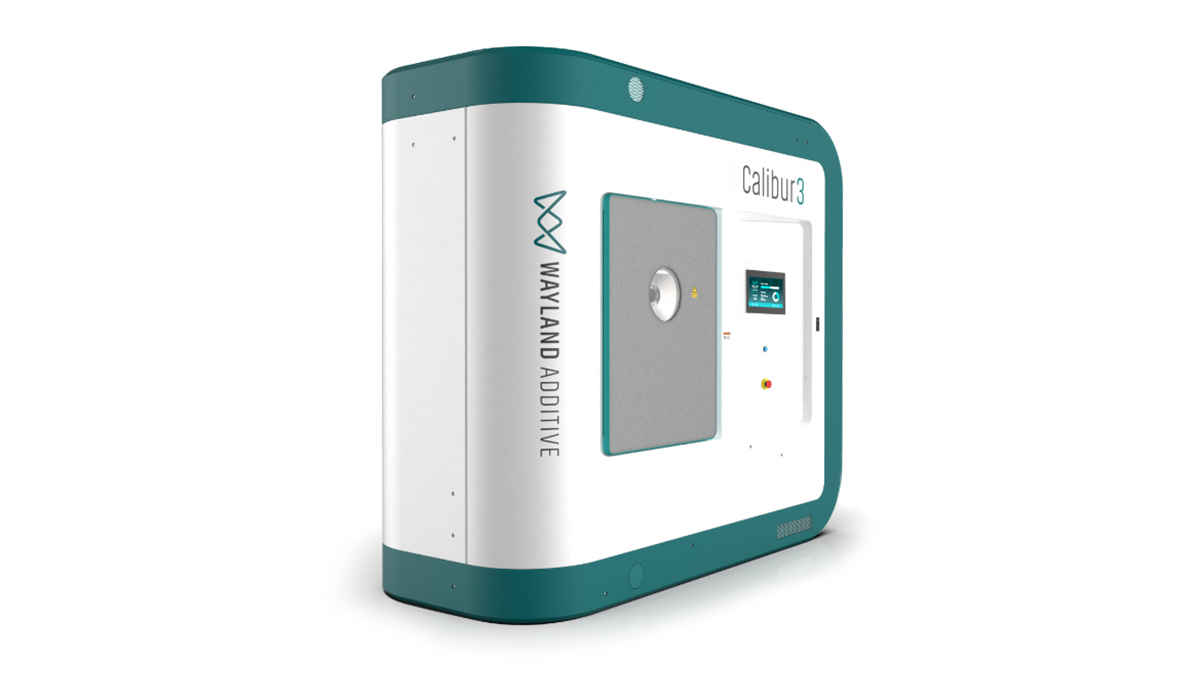
Another advantage of this technology is the monitoring feature during printing. Calibur 3 enables process monitoring with individual structured light scanning, electron imaging and high-speed infrared camera modules. With the monitoring feature for each part printed on the system; users can intervene in any stage of the printing process. This feature also saves time and cost reduction.